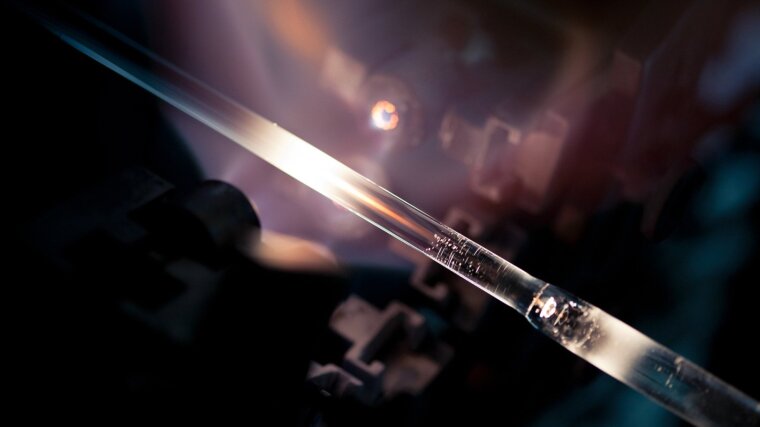
In the Optical Fiber Materials and Structures work group at Leibniz Institute of Photonic Technology (IPHT), fibres are being developed for hair-thin endoscopes of the future and other applications. After all, such fibres aren’t available »off the shelf« and fibres can be quite different.
By Ute Schönfelder
Many of the fibers for endoscopic holography are developed in-house. In doing so, the researchers rely on the expertise at their own institute. Dr Katrin Wondraczek and her team at Leibniz IPHT specialize in the production of core materials for optical glass fibres that are »tailor-made« depending on their intended application and functionality. »It’s a bit like baking a cake«, says the research group leader with a twinkle in her eye.
»Depending on the cake you want, we put together the right recipe«. Just like cakes in an oven, the fibre preforms consist of various glass elements that are »baked« into a fibre and then drawn out in ultra-fine dimensions. For example, a flexible fibre produced for endoscopic imaging consists of dozens of individual fibre cores with different optical properties. Such a hybrid fiber – that is, composed of different materials – is nevertheless only about 250 micrometers thick in the end: about four times the thickness of the nerve cells it images.
Cross-section of a packing of doped and undoped quartz glass rods in a cladding tube.
Image: Anne Matthes»Spaghetti bundles« extenden ten thousand times
But how are such ultra-fine fibres actually made? »The starting point for every glass fibre – regardless of its composition – is a glass rod known as a ›preform‹«, explains chemist Katrin Wondraczek.
»To make a preform, appropriately doped and undoped rods are combined to make a fibre with the desired design, although around 100 times thicker« It looks a bit like stacking glass spaghetti into a bundle a few centimetres thick. This »spaghetti bundle«, which is around half a metre long, is then drawn out into a fibre that can be several kilometres long.
»In this process, the preform material is scaled down«, explains Katrin Wondraczek. If the diameter of the fibre is a hundred times smaller than that of the preform, the length increases by a factor of 10,000. As an example, a preform that is one centimetre thick is turned into a fibre with a diameter of around 100 micrometres – the thickness of a human hair.
The preform element, the »spaghetti«, consist primarily of silica (SiO2), the common glass material. In order to create the function of specialty glass fibres, this base material is doped with additional substances. For example, ytterbium oxide is required for laser fibres, while data fibres usually contain germanium oxide. Katrin Wondraczek and her colleagues are now working on manufacturing doped glass in such a way that the doping agents are distributed as homogeneously as possible and are present in the exact concentration, which is crucial for the performance of the final glass fibre.
And here, at the latest, it becomes clear that the whole process is a bit more complicated than baking a cake. After all, when it comes to producing specialty glass fibres, selecting the right ingredients isn’t the only important factor. The manufacturing process itself is also critical for the end result. And contrary to what one might assume, the glass materials developed by Katrin Wondraczek and her team do not come from a melting furnace either. Rather, they are made from gaseous, liquid, or solid starting materials.
Dr Katrin Wondraczek and her team develop preforms for optical fibres.
Image: Lothar WondraczekMaking glass from gas
In the case of endoscopic fibres, for example, germanium-doped glass preforms are needed that are produced with Wondraczek’s team in a process known as »gas-phase deposition«.
This is where the initially liquid chemical »ingredients« – silicon and germanium chloride – are fed through a glass tube with oxygen in a stream of helium and heated under a flame of over 1,800 °C. In this process, they vaporize, react with oxygen and form SiO2 doped with GeO2. This substance is deposited as a very dry powder on the inner wall of the glass, where it is heated further until it »vitrifies«.
As the burner moves slowly along the tube during this process, a new glass layer grows inside. This tube is then collapsed into a glass rod: just about one centimetre thick and up to half a metre long.
»Compared to the traditional melting process, gas-phase deposition allows us to obtain glass rods with very homogeneous doping in the core area and high purity,« Wondraczek points out the main advantages of this technique. The materials produced using this method also have a very low attenuation loss, which is another crucial factor for their use in long data fibres. »However, the disadvantage is that we can only use gas-phase deposition to obtain glass rods with relatively small doped core areas of less than a centimetre in diameter, which limits the length and maximum core diameter of the fibres to be drawn from them«, adds Katrin Wondraczek.
Every fibre is unique
That’s why the glass scientists are also working on other alternatives. One process in which glass is also not made from a melt but from solid starting materials is the doping of existing SiO2 particles. As part of this method, known as »reactive powder sintering« (REPUSIL), silica nanoparticles and the required doping agents are processed into granular powder and pressed into solid cylinders.
These green bodies determine the shape and size of the resulting glass rod after sintering and vitrification. During sintering, the material is heated but remains under its melting point, causing it to become vitrified. As the glass rods obtained in this way can be several centimetres thick, fibres with very large cores can be drawn out and the fibres can be much longer than obtained from gas-phase deposition.
Regardless of how the preform is made, it ends up as a unique fibre, with an individual design, a specific composition and structure depending on whether it is a laser fibre or a fibre for data communication, imaging, or spectroscopy. And yet the development of a fibre begins with the same basic prerequisites: quartz, high temperatures and the right know-how.